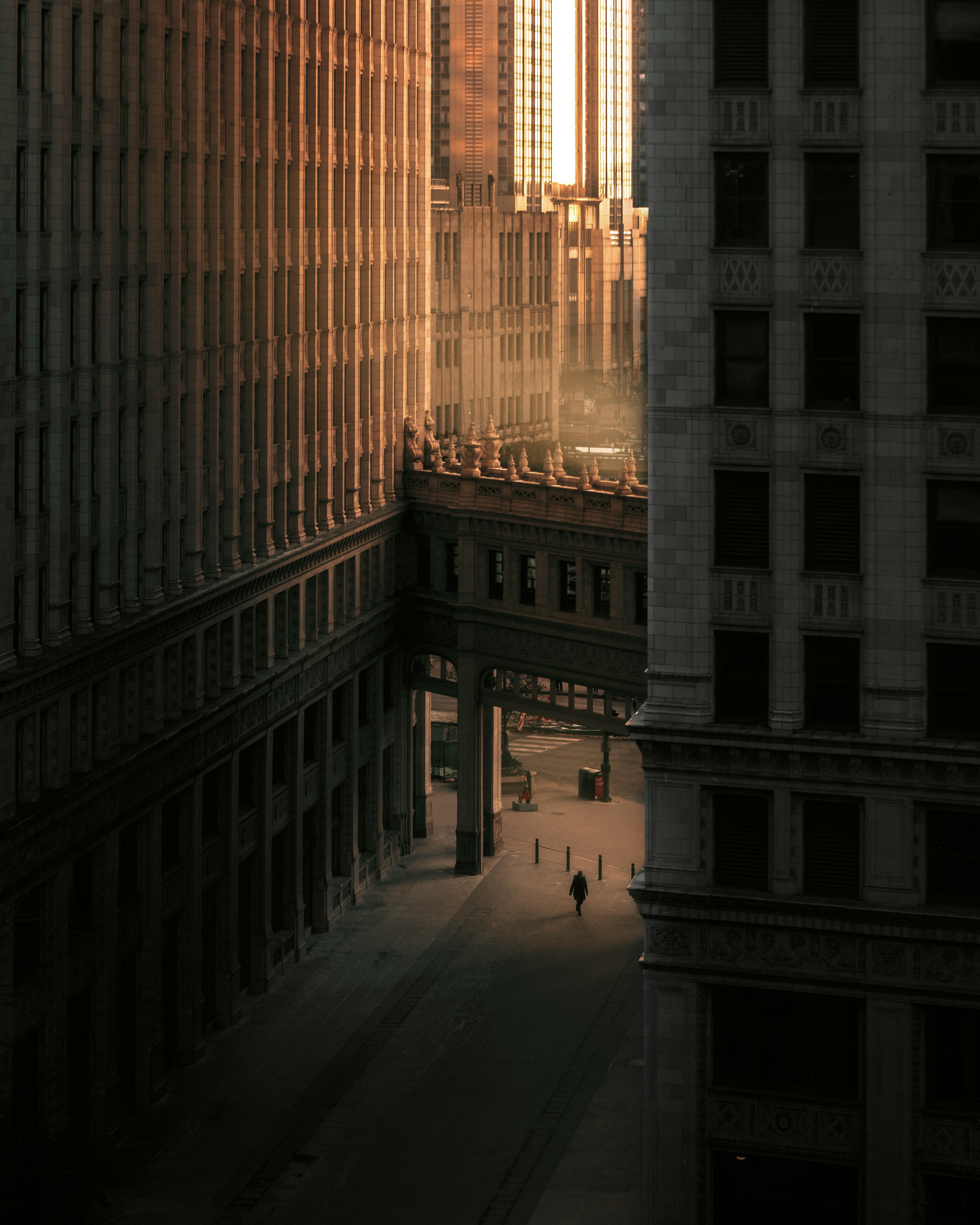
We consider the architecture industry as one of the most challenging fields today. Services offered by companies involved in the architectural space are always on high demand and being sought after by both corporate, government, and private individual clients.
One of the most sought out services here involves the creation of architectural models with tight deadlines. This one is incessantly in high demand.
Fortunately, the 3D printing Australian sector is a dynamic industry and essentially can help with this kind of need. Otherwise known as an additive manufacturing method, harnessing the potential of 3-dimensional printing for engineering and architectural space will make the lives of architects easier than they can ever imagine.
3D printing can help engineers and architects in creating intricately detailed miniscule models of their design ideas.
Why Use 3D Printing for Architectural Models?
3-dimensional printing makes it possible for architects and design engineers to come up with custom architectural models in no time and at a reasonable cost.
Before any 3D model can be 3D printed, you need to have a very detailed and complete 3D model first. By virtue of an accurate 3D model, we stand a good chance of having a good mastery of the level of details and desired visual simplifications.
What Material and 3D printing technology Is Ideal for Architectural Models?
Selective Laser Sintering or SLS is the most preferred 3-dimensional printing technology that has found practical application in 3D printing of architectural/structural models. Additive manufacturing companies often partner this with the raw Nylon PA12.
SLS allows the creation of 3-dimensional models that have a very close resemblance to proposed architectural designs. It can easily retain sharp edges and presents no issue when it comes to having clear openings. This is in complete contrast to 3D prints made with another additive manufacturing technology Fused Deposition Modeling or FDM technology.
With 3D printing Australia, you will not have a hard time making white architectural models.
This architectural modeling type is most often utilized for contests and helps you come up with your project’s simplified volumetry, without the need for any of its information to have anything to do with materiality.
What Value Does 3D Printing Australian Industry Bring to the Sector of Architecture?
Additive manufacturing, which is more popularly known as 3D printing has a wide spectrum of applications that brings value to architecture. Depending on purpose or needs, at any phase of a given architectural or engineering project.
If you want to make some fast progress in your designing phase, make use of 3-dimensional printing internally. Doing so will help you come up with a volumetry’s physical formalization on a certain scale. The said formalizations can take part in your iteration work. You have this when working on an architectural project.
If you are to make a presentation for an architectural project, you can make additive manufacturing or 3-dimensional printing take part in creating the architectural model of your conceptual design.
Simply put, 3D printing takes on an integral role when it comes to the production of prototypes or small-scale models of design for the building industry. It can also take an active role in building the building itself. The simplicity of its use and freedom of shape it is offering can significantly help in creating various architectural elements of the building in question.
It is safe to say that we have an awful lot of great possibilities in store for the 3D printing Australia industry. Most of which remain unknown but will soon unfold. Besides being a dynamic sector in the business world, 3-dimensional printing is also evolving according to our needs.